FANUC系统是一种比较完善、广泛用于车、铣、钻以及加工中心的数控系统,该系统加工性能稳定、加工精度高、操作灵活简便,能加工复杂多样的零件。本节介绍的BEIJING-FANUC
SERIES O-MD数控系统即是一种高精度、高性能的软件固定型的CNC数字控制系统。
一、机床操作面板简介
机床操作面板依据不同的CNC机床而不同,其开关的功能及排列顺序也各不相同。详细情况可参照机床说明书。图3-28为BEIJING-FANUC
SERIES O-MD数控系统的机床操作面板。
表3-2 BEIJING-FANUC SERIES
O-MD系统的操作功能键说明
名 称 |
用 途 |
循环起动键 |
自动运转的起动。在自动运转中,自动运转指示灯亮。 |
进给保持键 |
自动运转时刀具减速停止。 |
方式选择键 |
选择操作种类。 |
快速进给 |
刀具快速进给。 |
JOG步进进给 |
手动连续进给,步进进给。 |
手轮 |
手轮进给。 |
单程序段 |
每次执行自动运转的一个程序段。 |
跳过任选程序段开关 |
跳过任选程序段。 |
空运转 |
空运转。 |
返回参考点 |
返回参考点。 |
快速进给倍率 |
选择快进给倍率的倍率量。 |
步进进给量 |
选择步进1次的移动量。 |
紧急停止 |
使机床紧急停止。 |
锁住选择 |
选择机床锁住。 |
手动绝对 |
自动运转中插入手动运转时,选择是否将手动移动量加到绝对值寄存器中。 |
进给速度倍率 |
选择自动运转、手动运转中进给速度的倍率量。 |
JOG进给速度 |
选择手动连续进给速度。 |
选择手轮轴 |
选择手动手轮移动的轴。 |
选择手轮轴倍率 |
选择手动手轮进给中1个刻度移动量的倍率。 |
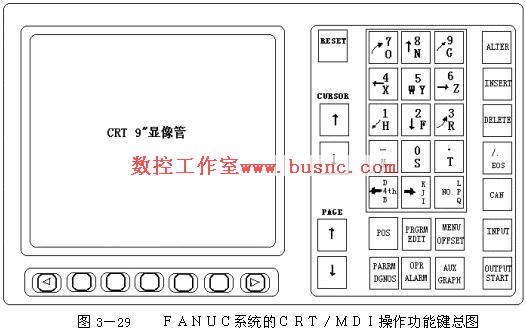
二、BEIJING-FANUC
SERIES O-MD系统CRT/MDI的操作功能键
BEIJING-FANUC
SERIES
O-MD系统CRT/MDI操作功能键主要分为二大部分,第一部分为是操作面板上的功能键,第二部分是操作面板上的数字输入及编辑键,参见图3-29。BEIJING-FANUC
SERIES O-MD系统的功能键有以下几种:
1.复位键(RESET键):用于解除报警,CNC复位。
2.启动键(START键):用于MDI运转的循环起动或自动运转的循环启动。也作地址或数字输出键(OUTPUT)。
3.
输入键(INPUT键):按地址键或数字键后,地址或数字进入键输入缓冲器并显示在CRT上。若要将缓冲器的信息设置到偏置寄存器中,可按INPUT键。此键作用与软键中的INPUT键等同。
4.取消键(CAN键):消除键输入缓冲器中的文字或符号。[例] 键输入缓冲器显示N0001时,若按[CAN]键,则N0001被取消。
5.光标移动键(CURSOR ↑、↓键):用小区分单位移动光标时使用。
6. 翻页键(PAGE ↑、↓键):翻动CRT页面时使用。
7.功能操作键:
[ POS ] 进行现在位置的显示。
[ PRGRM ] EDIT方式时,进行存储器内程序的编辑、显示;MDI方式时,进行MDI数据的输入、显示,自动运转中进行指令值的显示等。
[ MENU/OFSET ] 进行偏置量的设定与显示。
[ PARAM DGNOS ] 运行参数的设定、显示及诊断数据的显示。
[ OPR/ALARM ] 显示报警号
注意:按任何一个功能按钮和[ CAN
],画面的显示就会消失。之后再按其中一个功能键,画面会再一次显示。
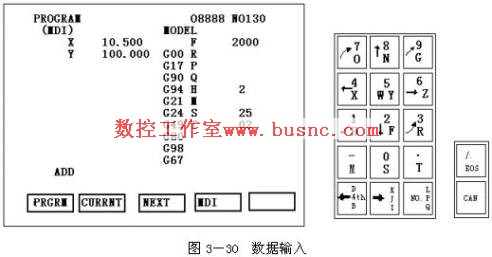
8.软键(参数NO.48 bit7设为1):软键按照用途可以给出多种功能,并在CRT画面的最下方显示:、
左端的软键[ ▲
] :由软键输入各种功能时,为返回最初状态(按功能键时的状态)而使用。右端的软键[
▼ ]:用于还未显示的功能。
9.BEIJING-FANUC SERIES O-MD系统的数据输入键为图3-30中右侧的数字键区,用于字母、数字等文字/地址的输入。
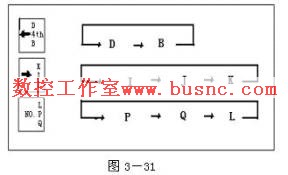
由数据输入键所输入的内容显示在画面下方倒数第2行。如图3-30所示,输入数据时,数据键和地址键兼用。对于在键面上印有多个地址的键([/,EOB]键、[D4thB]键、[IJK]
键、[PQL] 键),根据按键的次数可作如下变化:
键入[/,EOB]以外的地址时,需按一下[/,EOB],地址才能被输入,其他请参考图3-31。
其中在屏幕上显示ADRS.
时,才能输入地址。其中在屏幕上显示NUM或NO.时,才能输入数值。地址或数值的切换,根据具体条件(当前页面)等,由CNC自动进行。
三、BEIJING-FANUC SERIES O-MD系统的运转方式
BEIJING-FANUC SERIES
O-MD系统的运转方式可分为手动运转和自动运转。
1.手动运转
用手动可以连续地移动机床各轴。
1)手动返回参考点:
使方式选择开关置于JOG的位置上,并使返回参考点的开关置于ON状态。点动+X、(-X)、+Y(-Y)、+Z(-Z),使各轴向参考点方向JOG进给,返回参考点之后指示灯亮。
2)手动连续进给:
使方式选择开并置于JOG的位置,并选择移动轴
,机床在所选择的轴方向上移动(手动只能单轴运动)。选择JOG进给速度后,还要按快速进给按钮,才能手动快速进给(注:此时与G00快速定位相同)。
3)步进(STEP)进给(增量进给):
使方式选择开关置于STEP的位置,选择移动量及移动轴。若按一次轴选择开关,仅在轴方向上移动其规定的移动量。关断后再次接通时,又仅移动规定的移动位置。其中步进移动速度与JOG进给速度相同。若按快速进给按钮,变为快速进给。快速进给时,快速进给倍率有效。
4)手动手轮进给:
使方式选择开关置于HANDLE的位置,选择手摇脉冲发生器移动的轴。右转(+方向)或左转(-方向)转动手摇脉冲发生器,使机床微量进给。移动量可按手动倍率开关切换。用×10的移动量为10倍,用×100的移动量为100倍。
5)手动绝对值开关接通·关断(MANUAL ABSOLUTE):
用于确定是否将手动移动量加在绝对值上。开关接通时,坐标值改变手动移动部分,开关关断时坐标值不变。
2.自动运转
预先将程序存入存储器中,选择要运转的程序,将方式选择开关置于AUTO的位置,按循环起动键,循环起动灯亮,自动运转开始。
在自动运转中,还可以采取以下2种运转方式:
1)MDI运转方式。即由CRT/MDI操作面板输入一个程序段的指令并执行。首先选择MDI运转方式,使MDI成为当前状态,然后输入所需的数据及指令,按启动键,指示灯亮,机床开始执行自动运转。
2)单程序段运转方式。将单程序段开关置于ON,按启动键,指示灯亮,则按照已输入的程序指令段,机床开始执行自动运转。停止自动运转可以预先用程序在想要停止的地方输入停止指令,如程序停止(M00)、任选停止(M01)、程序结束(M02、M30)等指令,也可以按操作面板上的按钮使自动运转停止。
在程序运转中,按机床操作面板上的进给保持按钮,可使自动运转暂时停止。若按进给保持按钮,进给保持灯亮,循环起动灯灭,机床变为以下状态:
①执行暂停中,停止暂停状态;②机床移动时,进给减速停止;③ M、S、T的操作执行后停止。
由DRT/MDI的复位按钮、外部复位信号可使自动运转停止,呈复位状态。
若在移动中复位,机床减速后停止。
3.试运转
当需要进行机床程序的检测时,可采用试运转。该机床设置有全轴机床锁住开关、单轴机床锁住开关以及辅助功能锁住开关,此功能多用于程序的检测。
4.空运转
空运转中,不考虑程序指定的进给速度,而应为以下进给速度。
快速进给按钮ON/OFF |
程序指令为快速进给时 |
程序指令为切削进给时 |
快速进给按钮ON |
快速进给 |
JOG进给最高速度 |
快速进给按钮OFF |
JOG进给 |
JOG进给速度 |
四、系统编程操作
1.编辑存储操作
使当前状态处于EDIT方式,按PRGRM键输入地址O及程序号、程序指令,再按INSRT键,将程序存储。
2.程序调用操作
使当前状态处于EDIT和AUTO方式,按PRGRM键,输入地址O及程序号,按CURSOR↓键,可以检索到所需程序,FANUC系统检索程序号方法很多,使用时,可以参照系统说明书。
3.程序删除操作
不管是部分删除还是全部删除,首先都要选择EDIT方式,按下PRGRM键,输入地址O与程序号,按DELETE就可以删除所指定的程序段,如果是全部删除,只需输入9999EDLET即可。
4.参数设置
刀具长度、单位补偿量的设置:按OFSET按钮,让光标移向需变更的编置号,用数据输入键输入补偿量,按INPUT键,补偿量输入并显示出来。
五、系统安全操作系统安全操作
1.紧急停止(EMERGENCY STOP)
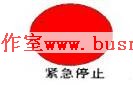
当发生紧急情况时,按机床操作面板上的紧急停止按钮,机床锁住,机床移动立即停止。紧急停止时,通向电机的电源被关断。解除紧急停止的方法随机床厂家而不同,一般通过旋转解除。解除紧急停止前,应排除不正常因素。
2.超程
刀具超越了机床限位开关规定的行程范围时,显示报警,刀具减速停止。此时,用手动将刀具移向安全的方向,然后,按复位按钮解除报警。
3.行程检测
图3-32所示,可设定刀具的移动范围。
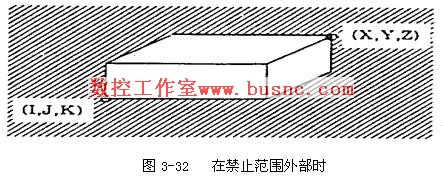
用参数设定限制范围,设定范围的外侧为禁止范围,通常由机床厂家一次在机床最大行程处设定,不需改变。但在设定禁止范围时,如果2点为同一点时,则所有领域均为禁止范围,且不必要的限位,应在机床行程范围之外设定。一旦到达禁止范围并报警后,只能从进入的方向退出。
4.报警处理
不能正常运转时,一般可按以下情况确认。1)
CRT显示错误代码时,可参照附录1
查找错误原因。P/S报警时,分析程序错误或设定数据错误,修改程序或重新设定数据。2)
CRT无显示错误代码时,可能系统正在进行后台处理,而运转暂时停止;如长时间无反应,可参照有关故障情况调查及故障检测办法,查明故障原因,对症处理。
|