对于车削加工,切入零件时采用快速走刀接近工件切削起始点附近的某个点,再改用切削进给,以减少空行程时间,提高加工效率。切削起始点的确定取决于毛坯余量的大小,以刀具快速走到该点时工艺系统内不发生碰撞为原则。加工螺纹时为保证加工精度,应有一定引入和引出距离。
在确定走刀路线时,应在保证加工精度和表面质量的情况下,使加工程序具有最短的走刀路线,不仅可节省工件的加工时间,还减少了一些不必要的刀具磨损及机床进给机构滑动部件的磨损等。
下面将简单介绍如何实现最短的空行程路线和最短的切削走刀路线。
1)合理设置起刀点
图5为采用矩形循环方式粗车的一般情况。其中图(a)将对刀点与起刀点设置在同一点,即A点,其走刀路线如下:
第一刀:A→B→C→D→A
第二刀:A→E→F→G→A
第三刀:A→H→I→J→A
图(b)则将对刀点与起刀点分离,设置为两点,即A点和B点,其走刀路线如下:
对刀点与起刀点分离的空行程为A→B
第一刀:B→C→D→E→B
第二刀:B→F→G→H→B
第三刀:B→I→J→J→B
显然采用图(b)所示的走刀路线,可以缩短走刀路线,提高加工效率。该方法也可用在其它循环车削(如螺纹车削)的加工中。
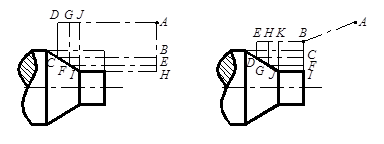
(a)
(b)
图5
合理设置起刀点
2)合理设置换刀点
为了换刀的方便和安全,可将换刀点设置在离工件较远的位置处,但会导致换刀后空行程路线的增长,所以可以在满足换刀空间的前提下将换刀点设置在较近点,则可缩短空行程距离。
3)合理安排“回零”路线
有时编程人员在编制较复杂零件的加工程序时,为尽量简化计算过程,便于校核程序,会使刀具通过执行“回零”指令,返回到对刀点的位置,然后再执行后续程序。这样就增加了走刀路线的距离,因此,在安排“回零”路线时,应使其前一刀终点与后一刀起点间的距离尽量缩短,或者为零,以满足走刀路线为最短的要求。另外,在选择返回对刀点指令时,在不发生加工干涉现象的前提下,应尽量采用X、Z坐标轴双向同时“回零”指令,该指令功能的“回零”路线将是最短的。
4)确定最短走刀路线
图6所示为零件粗车的几种不同切削走刀路线的安排示意图。其中图(a)表示封闭式复合循环功能控制的走刀路线;图(b)为
“三角形”走刀路线;图(c)为“矩形”走刀路线。这三种走刀路线中,矩形循环路线的进给总长度为最短。
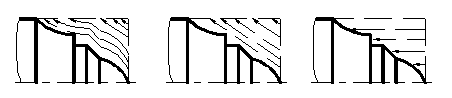
(a)
(b)
(c)
图6
粗车进给路线示例