目前数控机床刀具所采用的刀具材料,主要有高速钢、硬质合金、陶瓷、立方氮化硼和聚晶金刚石。
(1)高速钢
高速钢是一种加入了较多的钨、钼、铬、钒等合金元素的的高合金工具钢。高速钢具有较高的热稳定性、高的强度和韧性、一定的硬度和耐磨性,在600℃仍然能保持较高的硬度。按用途不同,高速钢可分为通用型高速钢和高性能高速钢。
通用型高速钢,广泛用以制造各种复杂刀具,可以切削硬度在250~280HBS以下的结构钢和铸铁材料。其典型牌号有W18Cr4V(称称W18),W14Cr4VMnXt,W6M05Cr4v2(简称M2),W9Mo3Cr4V(简称W9)。
高性能高速钢包括高碳高速钢、高钒高速钢、钴高速钢和超硬高速钢等。其刀具耐用度约为通有型高速钢刀具的1.5~3倍,适合于加工超高强度等难加工材料。其典型牌号有W2Mo9Cr4Vo8(M42),是应用最广的含钴超硬高速钢,具有良好的综合性能;W6Mo5Cr4V2AI和W10Mo4Cr4V3AI(5F-6)是两种含铝的超硬高速钢,具有良好的切削性能。
(2)硬质合金
硬质合金是将钨钴类(WC),钨钴钛(WC-TiC),钨钛钽(铌)钴(WC-TiC-TaC)等难熔金属碳化物,用金属粘结剂Co
或Ni等经粉未冶金方法压制烧结而成。
按照ISO标准以硬质合金的硬度、抗弯强度等指标为依据,将切削用硬质合金分为三类:P类(相当于我国的YT类)、K类(相当于我国的YG类)和M类(相当于我国的YW类)。
在ISO标准中,通常又在K、P、M三种代号之后附加01、05、10、20、30、40、50等数字进一步细分。一般说来,数字越小,硬度越高,韧度降低;数字越大,韧度提高但硬度降低。
涂层硬质合金刀具是在韧性较好的硬质合金基体上或高速钢刀具基体上,涂覆一薄层耐磨性高的难熔金属化合物而成的。常用的涂层材料有TiC、YiN、YiCN
、TiB2、ZrO2
及Al2O3等陶瓷材料。涂层可采用单涂层,也可采用双涂层或多涂层,涂层厚度一般为0.005~0.015mm。
硬质合金的涂层方法分为两类。一类为化学涂层法(CVD法),一类为物理涂层法(PVD法)。化学涂层是将各种化合物通过化学反应,沉积在工具表面上形成表面膜,反应温度一般在1000
℃左右。物理涂层是在550℃以下将金属和气体离子化后,喷涂在工具表面上。
硬质合金涂层一般采用化学涂层法(CVD法)生产。涂层物质以TiC最为广泛。数控机床上机夹不重磨刀具的广泛使用,为发展涂层硬质合金刀片开辟了广阔的天地。涂层刀具的使用范围广泛,从非金属、铝合金到铸铁、钢以及高强度钢、高硬度钢和耐热合金、钛合金等难加工材料的切削均可使用。实际加工应用中,涂层硬质合金刀片的耐用度至少可提高1~3倍
。涂层硬质合金的通用性广。
涂层高速钢刀具主要有钻头、丝锥、滚刀、立铣刀等。
因为涂层刀具有比基体高得多的硬度、抗氧化性能、抗粘结性能以及低的摩
擦系数,因而有高的耐磨性和抗月牙洼磨损能力,且可降低切削力及切削温度,所以在加工中可采用比未涂层刀具高得多的切削用量,从而使生产效率大大提高。
(3)陶瓷刀具材料
陶瓷刀具材料的品种牌号很多。按其主要成分大致可分为以下三类。
1)氧化铝系陶瓷
此类陶瓷的突出优点是硬度及耐磨性高,缺点是脆性大,抗弯强度低,抗热冲击性能差,目前多数用于铸铁及调质钢的高速精加工。
2)氮化硅系陶瓷
这种陶瓷的抗弯强度和断裂韧性比氧化铝系陶瓷有所提高,抗热冲击性能也较好,在加工淬硬钢、冷硬铸铁、石墨制品及玻璃钢等材料时有很好的效果。
3)复合氮化硅一氧化铝(Si3N4+Al2O3)系陶瓷
该材料具有极好的耐高温性能、抗热冲击和抗机械冲击性能,是加工铸铁材料的理想刀具。其特点之一是能采用大进给量,加之允许采用很高的切削速度,因此可以极大地提高生产率。
(4) 立方氮化硼(CBN)
立方氮化硼是靠超高压、高温技术人工合成的新型材料,其结构与金刚石相似。它的硬度略逊于金刚石,但热硬性远高于金刚石,且与铁族元素亲和力小,加工中不易产在切屑瘤。
(5)聚晶金刚石(PCD)
聚晶金刚石是用人造金刚石颗粒,通过添加CO、硬质含金、NiCr
、Si-SiC以及陶瓷结合剂,在高温(1
200℃)、高压下烧结成形的刀具,在实际中得到了广泛地应用。
上述几类刀具材料,从总体上来说,在材料的硬度、耐磨性方面,金刚石为最高,立方氮化硼、陶瓷、硬质合金到高速钢依次降低;而从材料的韧性来看,则高速钢最高,硬质合金、陶瓷、立方氮化硼、金刚石依次降低。下图显示了目前实用的各种刀具材料硬度和韧性排列的大致位置。涂层刀具材料具有较好的实用性能,也是将来实现刀具材料硬度和韧性并存的重要手段。在数控机床中,目前采用最为广泛的刀具材料是硬质合金。因为从经济性、适应性、多样性、工艺性等多方面,硬质合金的综合效果都优于陶瓷、立方氮化硼、聚晶金刚石。
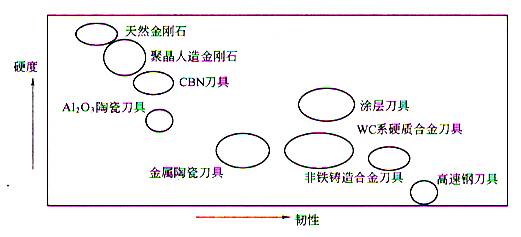